Dr.-Ing. Cooper Welch
Working area(s)
Contact
welch@rsm.tu-...
Automotive internal combustion engines (ICEs) play a critical role in modern society. As the world continues to develop, the number of ICEs in use will continue to grow. Increasing concerns about the sustainability of such a mode of transportation in areas such as fossil fuel consumption and harmful emissions have necessitated the need for new technologies and fundamental research in ICEs. Therefore, RSM aims to better understand the complex physical and chemical processes associated with ICEs.
The optically accessible research engine at TU Darmstadt (Fig. 1) uses an automotive engine with a quartz glass cylinder liner and piston for optical access. The optical engine operates under engine motored or fired and port fuel injection or direct injection conditions and allows a number of simultaneous diagnostics to be performed. Along with the acquisition of temperature and pressure, advanced optical diagnostic techniques including particle image velocimetry (PIV), laser-induced fluorescence (LIF), thermographic phosphor thermometry (TPT), Mie scattering imaging, diffuse back illumination (DBI), and tunable diode laser absorption spectroscopy (TDLAS) are used to gain insight into the fundamental characteristics of engine operation.
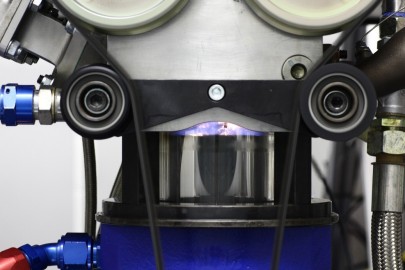

In-cylinder flows play an important role in the combustion process of spark ignition engines. Using the aforementioned methodologies, the interaction between the flow and the other combustion processes, namely direct injection spray morphology, spark discharge, and flame growth, are investigated. In particular, understanding the effects of different strategies for sustainable ICE combustion on cycle-to-cycle variations, such as exhaust gas recirculation, or renewable fuels, for example hydrogen, are critical for the energy transition of the near future.
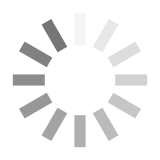
Error on loading data
An error has occured when loading publications data from TUbiblio. Please try again later.
-
{{ year }}
-
; {{ creator.name.family }}, {{ creator.name.given }}{{ publication.title }}.
; {{ editor.name.family }}, {{ editor.name.given }} (eds.); ; {{ creator }} (Corporate Creator) ({{ publication.date.toString().substring(0,4) }}):
In: {{ publication.series }}, {{ publication.volume }}, In: {{ publication.book_title }}, In: {{ publication.publication }}, {{ publication.journal_volume}} ({{ publication.number }}), ppp. {{ publication.pagerange }}, {{ publication.place_of_pub }}, {{ publication.publisher }}, {{ publication.institution }}, {{ publication.event_title }}, {{ publication.event_location }}, {{ publication.event_dates }}, ISSN {{ publication.issn }}, e-ISSN {{ publication.eissn }}, ISBN {{ publication.isbn }}, DOI: {{ publication.doi.toString().replace('http://','').replace('https://','').replace('dx.doi.org/','').replace('doi.org/','').replace('doi.org','').replace("DOI: ", "").replace("doi:", "") }}, {{ labels[publication.type]?labels[publication.type]:publication.type }}, {{ labels[publication.pub_sequence] }}, {{ labels[publication.doc_status] }} - […]
-
Number of items in this list: >{{ publicationsList.length }}
Only the {{publicationsList.length}} latest publications are displayed here.